In the landscape of modern business, one of the pivotal challenges faced by companies is to cater to the increasing demands of clients. As a business starts to witness a surge in orders, it becomes imperative to reevaluate and fortify the supply chain efficiency. The crux lies not only in meeting the escalating needs but also in ensuring sustainable quality and quantity. Engaging in comprehensive supply chain research emerges as a strategic maneuver to navigate through this scenario.
Understanding the Need for Supply Chain Research
A surge in client orders often catalyzes a re-examining of the supply chain efficiency. This critical juncture demands an in-depth exploration of existing manufacturing processes, suppliers, and distribution channels. By gaining an intimate understanding of every facet of the supply chain, businesses can identify the potential bottlenecks and inefficiencies that might hinder meeting heightened demands.
Identifying Suitable Factories
A core component of supply chain research is identifying and evaluating factories capable of meeting increased demands without compromising on quality or quantity. The search involves delving into a pool of potential suppliers, scrutinizing their production capabilities, quality control measures, and their commitment to sustainability. Opting for factories that align with sustainable practices not only contributes to ethical business conduct but also ensures a more enduring partnership in the long run.
In the pursuit of identifying factories capable of meeting increased demands without compromising quality or quantity, businesses employ a comprehensive set of criteria for assessment. These criteria encompass diverse aspects, including production capacity, quality control measures, and sustainability practices, among others.
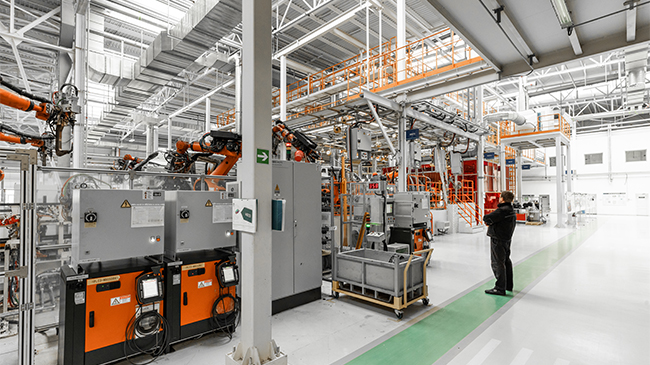
Criteria for Assessment:
- a. Production Capacity: This crucial factor gauges a factory’s ability to scale production to accommodate increased demands. It involves evaluating current output levels, production technologies, and the flexibility to adapt to varying order volumes.
- b. Quality Control Measures: Assessing a factory’s quality control protocols ensures consistent product excellence. This involves examining quality assurance processes, adherence to industry standards, and certifications such as ISO standards.
- c. Sustainability Practices: An increasingly pivotal aspect, sustainability practices encompass environmentally friendly manufacturing processes, ethical sourcing, waste reduction initiatives, and a commitment to reducing the carbon footprint. Evaluating these practices aligns with the growing demand for eco-conscious products.
Pressure for Competitive Pricing
Increasing the number of factories in consideration not only expands the options available but also exerts pressure on these factories to offer competitive prices. Healthy competition among suppliers often results in more favorable pricing for the purchasing company. This aspect is crucial in maintaining a competitive edge in the market while ensuring that the quality and quantity standards remain uncompromised.
Factors Influencing Factory Selection
While expanding the pool of factories can offer multiple benefits, the selection process involves a careful analysis of various factors. Beyond pricing and capacity, the focus should be on the factory’s track record, reliability, adherence to industry standards, ethical practices, and ability to scale operations in sync with the growing demands.
Evaluation Process:
- a. Reliability: Ensuring factory reliability is crucial in maintaining consistent and timely production. Factors such as historical performance, supplier relationships, and reviews from other clients play a pivotal role in assessing reliability.
- b. Scalability: Factories capable of scaling operations efficiently without compromising quality are highly sought after. This involves evaluating the ease with which a factory can adjust production levels in response to fluctuating demand.
- c. Adherence to Industry Standards: Compliance with industry-specific standards and regulations ensures adherence to quality benchmarks and ethical practices. This includes labor standards, safety protocols, and certifications within the industry.
2. Impact of Geographical Location:
The geographical location of factories significantly influences logistics and overall supply chain efficiency. Proximity to transportation hubs, ports, or raw material sources can streamline logistics, reduce transportation costs, and minimize lead times. Additionally, geopolitical stability and economic factors in the region can impact supply chain reliability.
For instance, a multinational electronics company strategically placed its factories in regions with access to skilled labor and efficient transportation networks. This decision not only optimized logistics but also facilitated faster order fulfillment and reduced shipping costs, ultimately enhancing the overall supply chain efficiency.
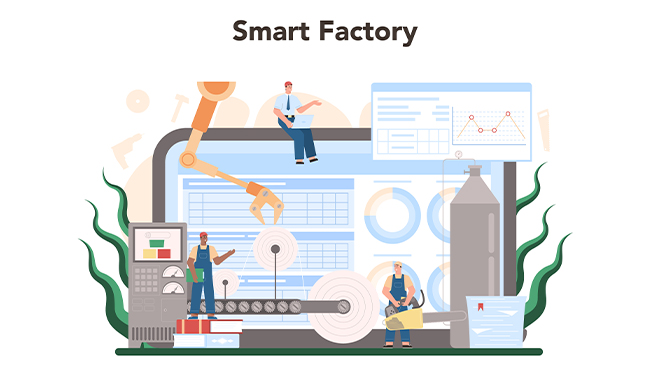
Striking the Balance Between Quality and Quantity
Meeting escalating client demands doesn’t merely entail increasing production volume. The key is to ensure that the surge in quantity doesn’t compromise the established standards of quality. A thorough assessment of potential factories aids in determining the right balance between quality and quantity, ensuring customer satisfaction remains unwavering.
- a. Process Optimization: Implementing lean manufacturing principles can streamline operations, eliminate waste, and enhance efficiency. This involves identifying and eliminating non-value-adding activities from the production process, thereby optimizing resources and ensuring quality remains paramount.
- b. Robust Quality Control Measures: Investing in comprehensive quality control measures is fundamental. This includes implementing stringent checks at various stages of production, utilizing state-of-the-art technology for inspection, and fostering a culture of quality consciousness among employees.
- c. Continuous Monitoring and Feedback Loops: Employing continuous monitoring mechanisms allows for real-time identification of issues or deviations from quality standards. Implementing feedback loops from customers, suppliers, and internal stakeholders aids in promptly addressing any quality concerns, enabling rapid corrective actions.
- d. Employee Training and Empowerment: Ensuring that employees are well-trained and empowered to make decisions regarding quality on the production floor is critical. Empowering workers to halt production in case of quality deviations fosters a proactive approach towards maintaining standards.
- e. Technology Integration: Leveraging technology, such as IoT-enabled sensors or AI-driven analytics, enables predictive maintenance, early defect detection, and optimized production processes, thereby ensuring quality while ramping up production.
Sustainable Practices in Supply Chain
In today’s conscientious market, sustainability is no longer an option but a necessity. Integrating sustainable practices within the supply chain is pivotal. Choosing factories committed to sustainable methods not only aligns with corporate responsibility but also caters to the growing demand from environmentally-conscious consumers.
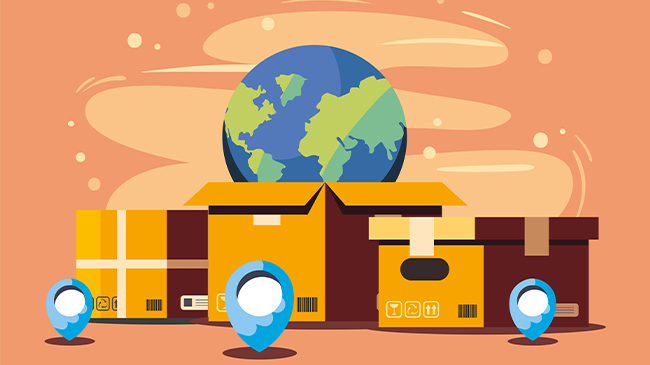
- a. Renewable Energy Usage: Transitioning towards renewable energy sources, such as solar or wind power, reduces carbon emissions and environmental impact during manufacturing processes.
- b. Waste Reduction and Recycling: Implementing waste reduction strategies and embracing recycling initiatives minimizes environmental footprints. This involves reusing materials, optimizing packaging, and adopting closed-loop systems to reduce waste generation.
- c. Ethical Sourcing: Ethical sourcing practices involve partnering with suppliers committed to fair labor practices, human rights, and ethical treatment of workers, ensuring a socially responsible supply chain.
- d. Circular Economy Principles: Embracing circular economy principles focuses on reducing resource consumption by designing products that can be reused, remanufactured, or recycled at the end of their lifecycle.
- e. Successful Implementation Examples: A multinational consumer goods company revamped its supply chain by collaborating with suppliers dedicated to sustainable practices. By encouraging responsible sourcing of raw materials and optimizing transportation, they not only reduced carbon emissions but also experienced cost savings and enhanced brand reputation due to their commitment to sustainability.
Another example is a fashion retailer that incorporated sustainable materials into its product lines and redesigned packaging to be more environmentally friendly. This initiative not only resonated with environmentally conscious consumers but also reduced waste and contributed to a positive brand image.
Benefits of a Diversified Supply Chain
A diversified supply chain doesn’t just mitigate risks associated with over-reliance on a single source; it also fosters agility and resilience. The ability to tap into multiple factories enables businesses to adapt swiftly to market fluctuations, disruptions, or unforeseen circumstances, thereby safeguarding against potential supply chain disruptions.
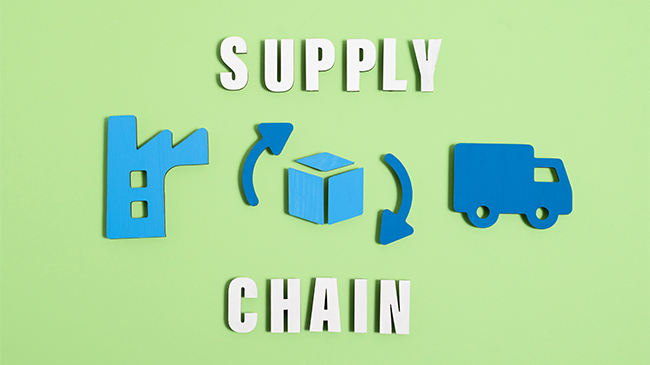
1. Risk Mitigation in Times of Uncertainty:
During times of crisis or disruptions, a diversified supply chain spreads risks across multiple suppliers and geographical locations. For instance, if one supplier faces production delays or geopolitical issues, alternate sources can compensate, preventing significant disruptions in the supply of goods or services.
2. Flexibility to Navigate Market Fluctuations:
Market fluctuations, whether due to changes in consumer preferences or economic conditions, can impact the demand and supply dynamics. A diversified supply chain allows businesses to adjust more swiftly by tapping into alternative suppliers or adapting to different market conditions without compromising on meeting client demands.
3. Challenges in Managing a Diverse Network:
Despite the advantages, managing a diverse network of suppliers presents challenges. One such challenge is maintaining consistency in quality across multiple sources. Variations in production methods, standards, or geographic disparities might lead to quality inconsistencies.
Solutions to Maintain Consistency:
To address these challenges, companies can implement stringent quality control protocols and standardized processes across all suppliers. Regular audits, clear communication of quality expectations, and providing necessary support and training to suppliers can ensure uniform quality standards across the supply chain.
Technology as an Enabler
Leveraging technological advancements plays a pivotal role in streamlining supply chain operations. From employing data analytics to optimize production and inventory management to implementing AI-driven forecasting models, technology paves the way for enhanced efficiency and informed decision-making within the supply chain.
1. Technological Tools for Optimization:
- a. Blockchain for Traceability: Blockchain technology enables transparent and immutable tracking of products throughout the supply chain. It ensures traceability, authenticity, and reduces the risk of counterfeit products.
- b. IoT for Inventory Management: Internet of Things (IoT) devices facilitate real-time tracking of inventory, enabling better inventory management, demand forecasting, and minimizing stockouts or excess inventory.
- c. Predictive Analytics for Demand Forecasting: Utilizing advanced analytics and machine learning algorithms aids in predicting demand patterns accurately. This allows for better inventory planning and more informed decision-making.
2. Integration into Supply Chain Processes:
- These technologies can seamlessly integrate into existing supply chain efficiency processes through robust system integrations and collaborative platforms. For instance, implementing blockchain-enabled systems for traceability can be integrated into existing ERP (Enterprise Resource Planning) systems.
- IoT devices can be integrated with inventory management systems to automate data collection and analysis, providing actionable insights. Similarly, predictive analytics can complement existing forecasting models to enhance accuracy and efficiency.
Conclusion
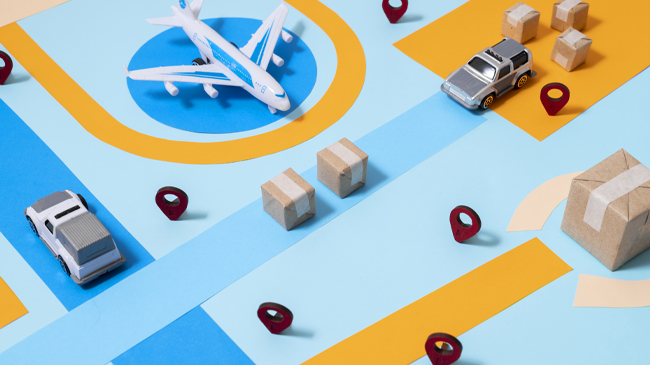
In today’s competitive business landscape, meeting growing client demands while upholding quality and sustainability hinges on a robust supply chain strategy. Thorough research, selecting suitable factories, and embracing sustainability are pivotal.
Balancing quality and quantity requires careful factory evaluation, stringent quality control, and leveraging technology. Diversifying the supply chain mitigates risks but managing multiple sources poses challenges, demanding uniform quality standards.
Technological tools like blockchain, IoT, and predictive analytics bolster efficiency. Integrating these seamlessly into the supply chain ensures adaptability and informed decision-making.
In summary, an agile, sustainable, and tech-driven supply chain is crucial. Embracing these principles ensures growth, resilience, and customer satisfaction in a rapidly evolving business world.
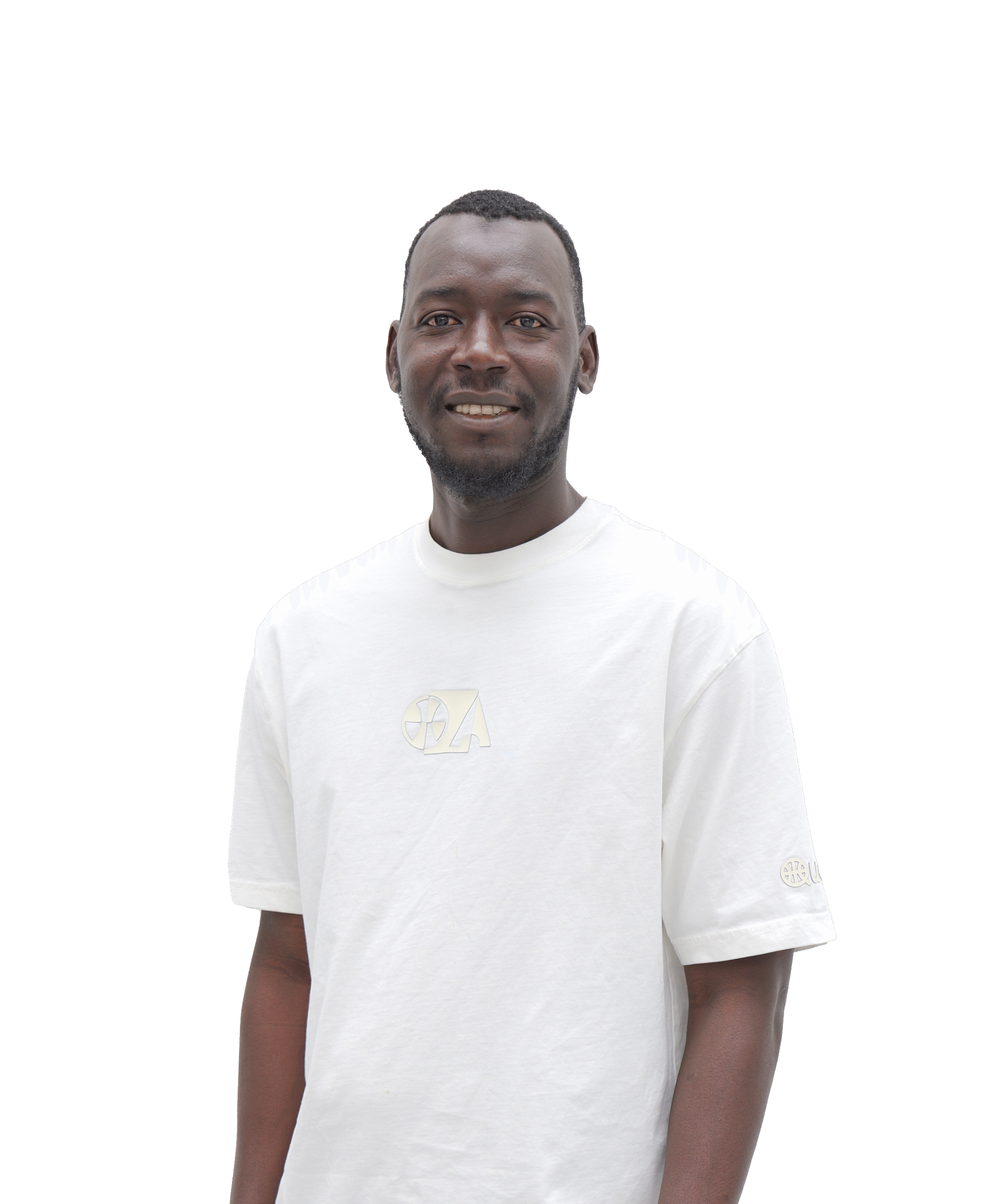
I’m Sackod, the business development lead at DSCP. I focus on helping experienced dropshippers solve real fulfillment problems — from U.S. warehouse operations to supply chain optimization — with a hands-on, transparent approach.